A thermoformed blister sealed on to a printed paper board is most common packaging for consumer goods. It can be tooth brush, a shaving razor, an SD card, a head phone or a Toy. It is very easy to display on shelves, and easily catches the attention of shoppers. Marketing information and instruction to use can be easily printed. Unlike the clamshell packaging, the blister packaging is easy to open. The only disadvantage is it cannot be used for a heavier product where the clamshell is the method of choice. The thermoplastic material most commonly used is APET. However PETGAG and PETG are used when better transparency is required. PVC which was used extensively in the past is being replaced with PET due concerns regarding its impact on environment.
There are different methods used to seal a thermoformed blister packaging to a printed paper board. RF sealing is preferred when automated lines that are operated at high speeds for large volume output. Pressure sealing using pressure sensitive adhesives is used for very small volume runs and has comparatively weak seal strength. Heat sealing of blister against the board is the most common method and is suited for both small and larger volumes. The tips to avoid seal failure during the expected storage life or the product are discussed below.
- Plastic material and the coating on the board: these have to be compatible and the coating should be uniform and with specified thickness.
- Sealing jigs: Maintain proper knurling and flatness regularly inspect for dirt and residues.
- Ensure that formed blisters are sampled and inspected for internal stress under polarized light.
- Sealing temperature, dwell time and pressure: These parameters have to be validated for a project and should not be changed without revalidating.
- Paper board cards have to be stored with proper packaging to avoid ingress of moisture especially under high humid conditions.
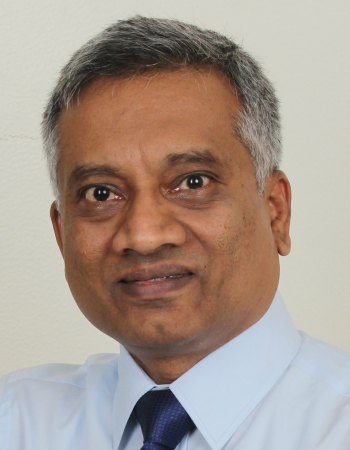
Muraleedharan Paloran,
Founder & CEO
Very good.