Additive manufacturing or 3 D printing is fabrication of an object layer by layer by depositing the material. Adapting this process into the design of thermoformed part or packaging can significantly shorten the time required for producing a prototype for testing and validation. Using the Model created by the software the printer builds a prototype mold and samples are made for testing. A process that could have taken 3 to 5 days can be completed within few hours. 3 D printed molds can be modified using conventional process. This is a very important advantage as some times during initial testing a small flaw in the design were noticed. Instead of printing another mould, such corrections are done by conventional method to save cost.
3 D printed moulds are porous and thus make it easy to form parts without the additional step of putting vents for evacuation. This advantage further shortens the time to make it ready. In contrast the conventional method requires the aluminum to be machined in a milling machine followed by drilling vent holes. 3 D printed molds are less costly and thus give the opportunity to test different design options without incurring too much expenditure or time. When developing packaging for consumer goods such a toy or an electronic gadget, this is a very handy tool, as the aesthetics and appearance of the packaged product on the shelf can be evaluated during design phase. Packaging created using contrasting orientation of the item within the package are kept on the shelf and graded by judges from target customer groups. The whole process of evaluation and finalizing the design and launching the product can be done in a matter of days than months with a fraction of the cost when compared to conventional method.
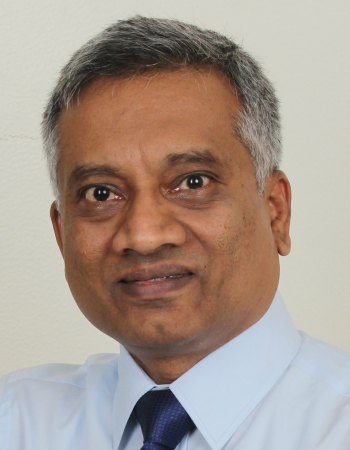
Muraleedharan Paloran,
Founder & CEO