MEDICAL DEVICE PACKAGING
PACKAGING FOR TERMINALY STERILIZED MEDICAL DEVICES
For Medical Device Packaging product protection is required throughout entire life including: sterilization, shipping, storage handling and use. Problems that can occur are: Protection from shock and vibration, crushing, puncturing, tearing, bursting, splitting, humidity, pin holing, heat etc.
PACKAGING DEVELOPMENT
Medical devices have short life cycles driven by innovations in the related technology of its manufacturing and feedback from the medical practitioners. Our designers can work with you during product development stage with designing, prototyping and testing of Medical Device Packaging for a new or improved product line.
COVERS BOTH HIGH RISK AND LOW RISK DEVICES
Medical Devices are a Surgical retractors, Hypodermic needles, Suction equipment, lung ventilators, Bone fixation Plates, Orthopedic Implants, Catheter or a heart valve. The maintenance of sterile barrier system (SBS) is distinctive characteristic of Medical device packaging. In many cases it should facilitate sterilization of the device within. Protective characteristics can be achieved through our Thermoformed Plastic Packaging by preventing the product from shifting or to keep the kit components separated or nested.
GMP COMPLIANT
Primary packaging that are in direct contact with medical devices such as implants must be manufactured under strict GMP with controlled environment. Particle counts in the manufacturing space are controlled to keep within the specifications. PETG made from medical grade resin is the basic raw material. Any additives used are also medical grade. PETG is superior to other thermoplastics in its ability to withstand ETO sterilization. Besides it has superior clarity and physical properties. We specialize in optimizing the package to ensure the numbers of packaging components are optimized to control packaging cost and inventory of packaging items.
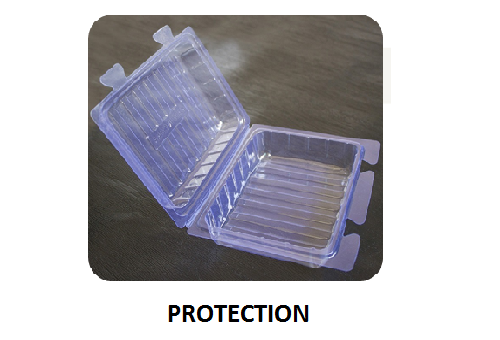
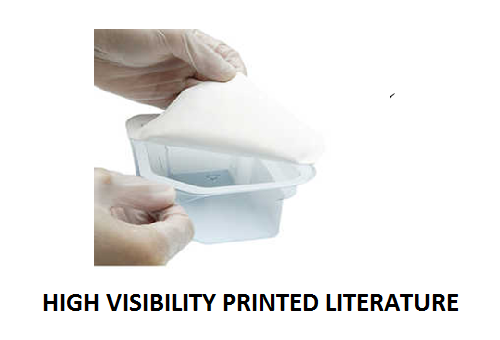
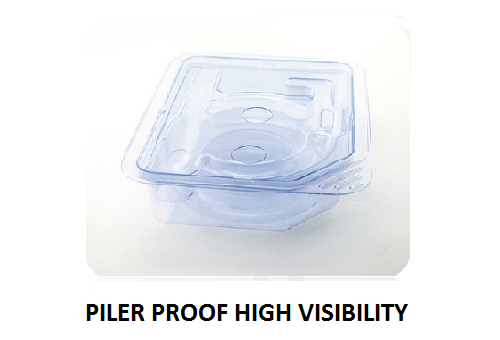
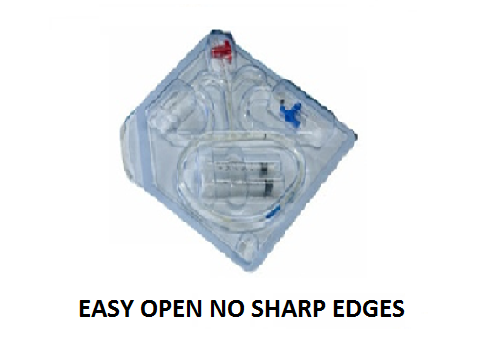