Majority of thermoplastics used in the manufacture of packaging (HIPS, PVC, PET, PP) are made from feed stocks obtained during refining of crude oil. These materials are very durable and inert to chemicals or environmental factors. This property makes these, the material of choice for packaging, the primary function of which is to protect its contents. However, the down side is that, the petrochemical derived thermoplastics are also very difficult to degrade, of at all, through the natural process. This is the cause of the well known problem of environmental pollution due to plastics. During natural process of degradation microorganisms present in the environment, consume the material converting it into its own biomass and breaking down the material into basic chemicals such as water, carbon dioxide and minerals. Bio Plastics are polymers which can be degraded through this natural way.
PLA is produced from Lactide monomer, which in turn is derived from lactic acid made through fermentation of corn starch. PLA can be hydrolyzed back to lactic acid. Further the material properties of PLA can be tailor made by using additives. PLA can be extruded into plastic sheets which can then be thermoformed using the regular equipments as in petrochemical based thermoplastics. Common applications where PLA can be used are Packaging for dairy products, Ready to eat food packaging, Clear blister packaging and drink cups for cold beverages. The packaging made from PLA has good aesthetics and high mechanical strength similar to that made from APET. It has better heat seal-ability which is an edge over APET. The permeability or barrier properties are comparable to APET.
Thermoformed trays and bowls made of PLA are ideal for food packaging such as those for chilled fresh products such as fruits, vegetables and salads. Natural antimicrobial such as Nisin can be incorporated into the sheet during extrusion to impart antimicrobial property to the package and increase the shelf life of the product.
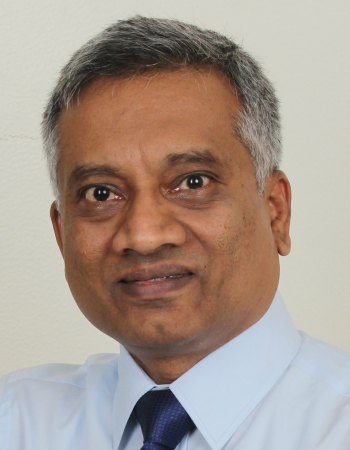
Muraleedharan Paloran,
Founder & CEO